Erfolgsgeschichten
Digitale Transformation
IT-Systemlandschaft für die Mediaprint Smart Factory
„Durch den maximalen Automatisierungsgrad reduzieren wir die komplexität der Produktion“
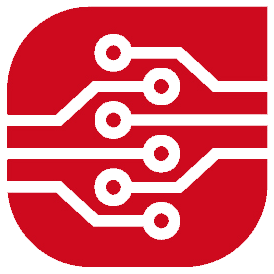
Komplexe Lagersituation
Flexible Nutzung von Anlagen und Geräten
Das projekt in 2 minuten erklärt
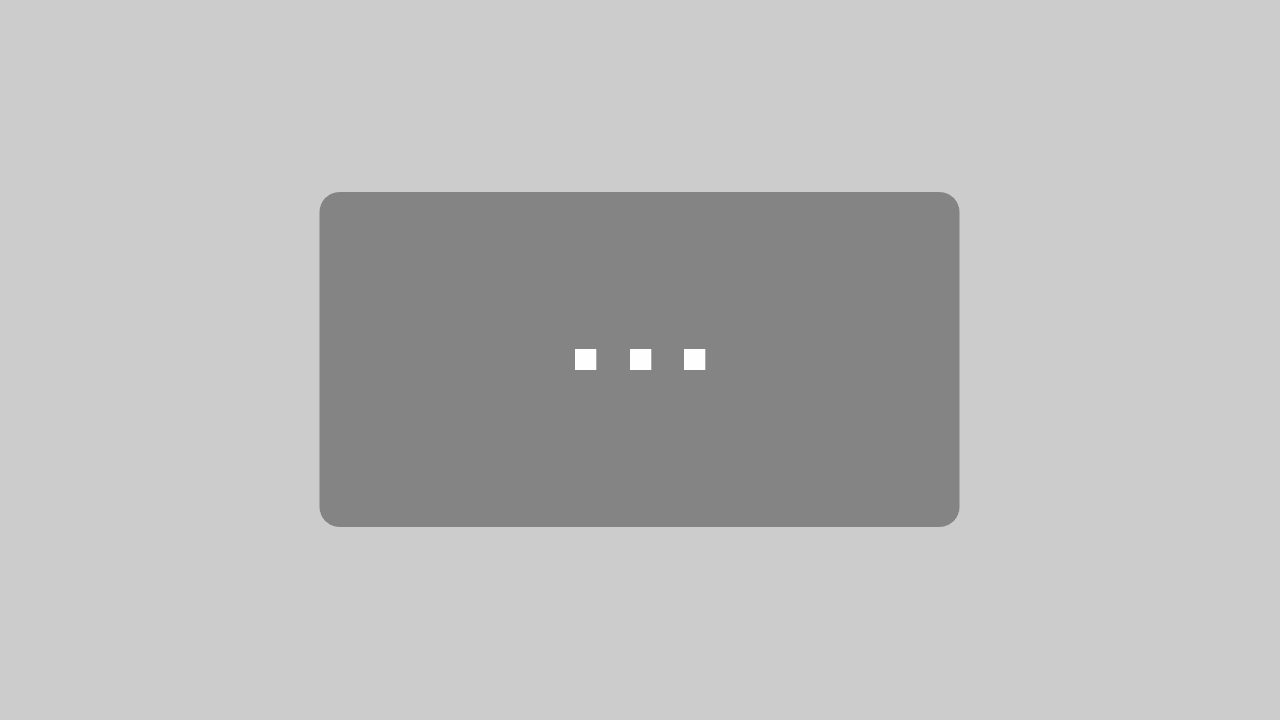
Mit dem Laden des Videos akzeptieren Sie die Datenschutzerklärung von YouTube.
Mehr erfahren
Foto: Fraunhofer IML
Interview
Ziele und Herausforderungen
1. Warum haben Sie sich zum Bau der Mediaprint Smart Factory entschlossen?
Tobias Kaase:
Unsere Branche steht vor großen Herausforderungen. Mass-Customization und lagerlose Echtzeit-Produktion sind zwei Trends, die die Druckproduktion nachhaltig prägen werden. Darauf müssen wir reagieren, um uns zukunftssicher aufzustellen. Hierzu haben wir uns intensiv mit unserer strategischen Ausrichtung beschäftigt. Zu dieser gehört die mediaprint smart factory: Mit ihr entsteht auf 1.800 Quadratmetern eine weitgehend vollautomatisierte Produktionsstätte für Commodity-Produkte. Hier werden wir in Zukunft Bücher in Kleinauflage und Auflage 1, Kataloge und Technische Produktinformationen, Wandkalender und Broschüren fertigen.
Dominik Haacke:
Commodity- sowie Customized-Print sind unsere beiden Standbeine. Wir sind als Customized-Druckerei groß geworden, also mit der Fertigung maßgeschneiderter, sehr komplexer Produktvarianten. Gleichzeitig gehört mit Commodity-Print die Produktion hoch standardisierter Druckerzeugnisse zu unserem Portfolio. Die klassische Druckproduktion und diese standardisierte Druckproduktion sind zwei völlig unterschiedliche Welten mit ganz anderen Anforderungen, die bei uns bisher in einer Produktion vereint waren. Mit der Mediaprint Smart Factory bekommen Commodity-Produkte ihr eigenes Zuhause – und unsere beiden Produktlinien auch nach außen ein eigenständiges Gesicht.
2. Welche Vorteile bringt das mit sich?
Dominik Haacke:
Wir können unsere Prozesse gezielt auf die Anforderungen der jeweiligen Druckproduktion ausrichten. Die mediaprint smart factory ermöglicht uns den hochindividuellen Druck innerhalb des standardisierten Produkt- und Materialkatalogs. Dabei setzen wir auf voll automatisierte Prozesse: Die Maschinen sind untereinander vernetzt, die innerbetrieblichen Transportprozesse automatisiert und die Kunden per API angebunden.
Tobias Kaase:
Durch den maximalen Automatisierungsgrad reduzieren wir die Komplexität der Produktion hinsichtlich der Bedienung der Maschinen sowie der Betriebsdatenerfassung. Zudem können wir die Produktionszeiten verkürzen und flexibel auf die tägliche Kapazitätsauslastung reagieren. Insgesamt ermöglichen uns diese Maßnahmen, auch kleine Losgrößen qualitativ hochwertig und zugleich kostengünstig zu fertigen.
3. Mit welchen Herausforderungen war der Aufbau dieser neuen Produktionslandschaft verbunden?
Dominik Haacke:
Die genaue Definition des Produktionsprozesses von der Bestellung bis zum Versand war eine komplexe Aufgabe. Wie soll die Arbeitsgestaltung aussehen? Wie können die einzelnen Produktionsschritte zusammenlaufen? Was für IT-Systeme benötigen wir, um diese automatisierte Produktion umzusetzen? Digital in NRW hat uns im Rahmen der Umsetzungsbegleitung sehr geholfen, Antworten auf diese und viele weitere Fragen zu finden – in Workshops und zahlreichen Gesprächen.
Tobias Kaase:
Die Experten des Kompetenzzentrums um Projektleiter Robert Joppen haben in enger Abstimmung mit uns die Soll-Prozesslandschaft und Datenlandkarte für die Smart Factory aufgenommen. Es wurden Anforderungen und Abläufe festgelegt, ein Lastenheft von uns erstellt und kompatible IT-Systeme ausgewählt.
4. Was sind jetzt die nächsten Schritte?
Dominik Haacke:
Wir haben nun eine professionelle Grundlage, um das passende System und entsprechende Module auszuwählen. Wir stimmen uns in einem nächsten Schritt mit unseren Partnern ab und ziehen auch Experten aus der Druckindustrie hinzu, um mögliche blinde Flecken in der entwickelten Systemlandschaft zu vermeiden. Auch Digital in NRW wird das Projekt weiterhin mitbegleiten.
5. Wie hat sich die Zusammenarbeit mit dem Kompetenzzentrum gestaltet?
Tobias Kaase:
Sehr gut und sehr professionell. Digital in NRW bringt viel Expertise und eine umfassende Sicht „von außen“ mit, die uns bei der Entwicklung dieser neuen Prozesslandschaft sehr weitergeholfen hat.
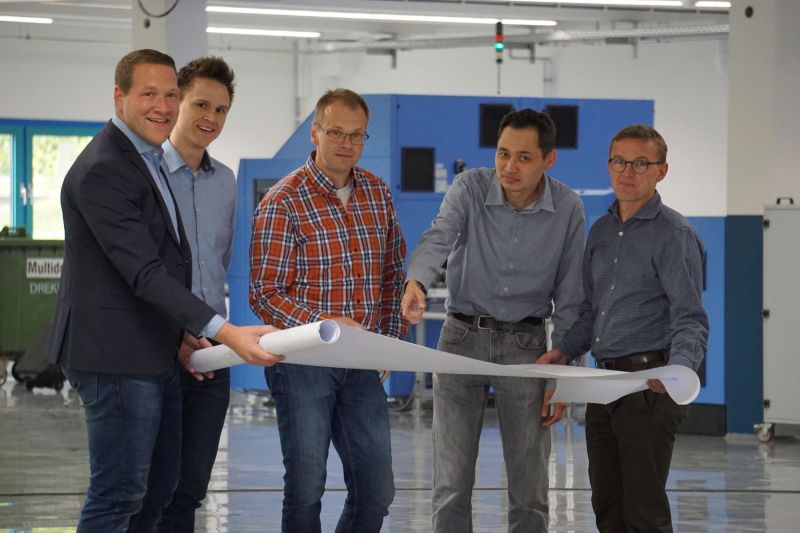
Gemeinsam arbeitet das Projektteam von mediaprint und Digital in NRW an den nächsten Schritten. © mediaprint solutions GmbH
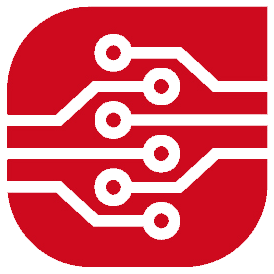
Der Kundennutzen
Was haben Sie davon?
Ihr Kundennutzen
- Wissensbasis zu relevanten Technologietrends der Antriebstechnik
- Methodische Unterstützung für die Arbeit mit dem Technologietrend-Radar
- Identifikation des zukünftigen Forschungsbedarfs als Grundlage zur zielgerichteten Initiierung von Forschungsprojekten
- Förderung des Wissenstransfers innerhalb des Forschungsnetzwerks
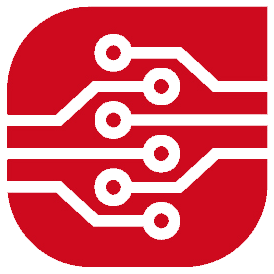
Der Kundennutzen
Was haben Sie davon?
Ihr Kundennutzen
- Wissensbasis zu relevanten Technologietrends der Antriebstechnik
- Methodische Unterstützung für die Arbeit mit dem Technologietrend-Radar
- Identifikation des zukünftigen Forschungsbedarfs als Grundlage zur zielgerichteten Initiierung von Forschungsprojekten
- Förderung des Wissenstransfers innerhalb des Forschungsnetzwerks