Erfolgsgeschichten
Digitale Transformation
Familienunternehmen setzt auf datenbasierte Verbesserung der Produktionstransparenz
DAISY: Digital in NRW und Horstmann GmbH entwickeln neues Tool
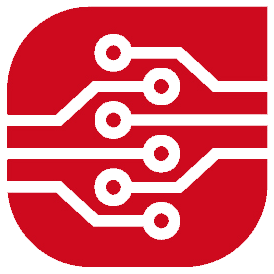
Die Lösung für Kennzahlen
Produktionsplanung
Eine Antwort auf variable Losgrößen
Bisher erfolgte die Produktionsplanung und -steuerung in dem Familienbetrieb größtenteils auf Basis jahrelanger Expertise, technischem Know-how und handschriftlichen Aufnahmen. Eine Zusammenführung von Kennzahlen und tägliche Auswertung war nur schwer möglich, wurde aber durch die Diversität in der Produktpalette, die in unterschiedlichen Produktionsbereichen mit verschiedenen Losgrößen in einem recht dynamischen Umfeld gefertigt wurden, zunehmend notwendig.
User Stories
Simple und wirkungsvoll: das KISS-Prinzip
Eine besondere Herausforderung
Neues Tool: DAISY
Soll- und Ist-Kennzahlen
Aktuelle Kennzahlen auf einen Blick
Weitere Bereiche des Unternehmens
DAISY Chain
Zukünftig soll die Anwendung auch auf weitere Bereiche des Unternehmens ausgeweitet werden: Mit DAISY Chain wurde das Konzept bereits weiterentwickelt. Diese Anwendung soll zukünftig den Prozess eines Auftrags durch die Fertigung sowie die Auslastung einzelner Fertigungsprozesse erheben. Seth Schmitz: „Um dies zu erreichen soll die DAISY-Technologie an jeder Arbeitsstation implementiert werden.“
Sie wollen ebenfalls eine Erfolgsgeschichte schreiben?
Dann schreiben Sie doch zuerst einmal uns.