Erfolgsgeschichten
Künstliche Intelligenz
KI-gestützte Zustandsüberwachung im Aluminium-Druckguss
Pilotprojekt: Vorhersagen für die Instandsetzung
Verschleiß feststellen, frühzeitige Wartung planen, Ausfälle vermeiden: Mit einer lückenlosen Zustandsüberwachung technischer Bauteile können Industriebetriebe unvorhergesehenen Störungen aus dem Weg gehen. Dabei erfassen an den Maschinen angebrachte Sensoren bestimmte Daten, etwa Temperatur, Schwingungen oder Lautstärke. Ein KI-Algorithmus kann in den Datenreihen Muster erkennen, die eine erhöhte Ausfallwahrscheinlichkeit erwarten lassen. Ab einer gewissen Wahrscheinlichkeit werden die Teile dann ausgetauscht. Die Weier GmbH aus Drolshagen hat sich auf die Instandsetzung von zylindrischen Bauteilen spezialisiert. In Kooperation mit dem Mittelstand-Digital Zentrum Ruhr-OWL wurde ein Transferprojekt umgesetzt, in dem die Partner eine Zustandsüberwachung von kundenseitig eingesetzten Füllkammern pilotiert haben.
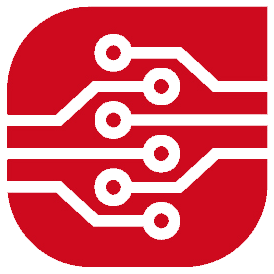
Digitalisierung als Herausforderung
Nachhaltigkeit durch Wiederverwendung
Instandsetzung im Aluminium-Druckguss
Schmelzen, füllen, und – Schuss: Bis zu 1.400-mal am Tag werden Aluminium-Druckgussfüllkammern eingesetzt, um flüssiges Metall unter Hochdruck in Stahlformen zu schießen. Die Weier GmbH, einst eine kleine Eisenwarenfabrik, gilt heute als führend in der Instandsetzung solcher Füllkammern, insbesondere im Aluminium- und Magnesiumdruckguss. Damit bietet Weier eine nachhaltige Alternative zur Neuanschaffung von Bauteilen.
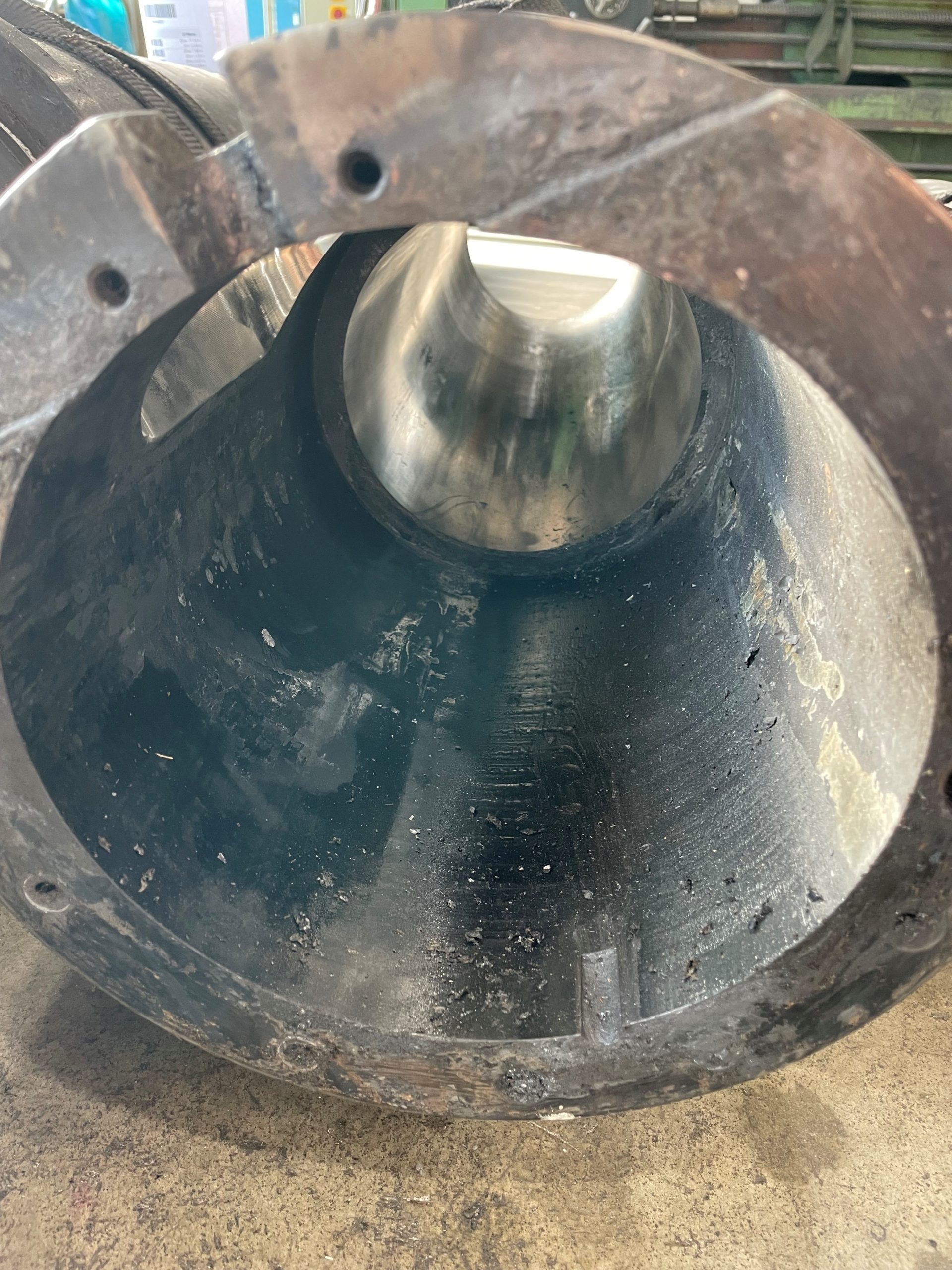
Verschlissene Druckgusskammern wie diese hier setzt die Weier GmbH wieder instand. Den richtigen Zeitpunkt dafür soll demnächst eine KI vorhersagen. (Foto: Weier GmbH)
Geschäftsmodell erschließen
Verschleiß von Füllkammern vorhersagen
Aluminium-Druckgussfüllkammern unterliegen durch die ständige Belastung einem natürlichen Verschleiß. Diese Schäden führen bei den Kunden zu ineffizienten Prozessen, minderer Produktqualität und außerplanmäßigen Wartungskosten in der Größenordnung mehrerer Tausend Euro – teils mehrmals die Woche. Bislang konnte dieser Verschleiß nur vage vorhergesagt werden. Hier setzte das Projekt an: Ziel war es, ein System zu entwickeln, das den Zustand der Füllkammern überwacht und frühzeitig Verschleißanzeichen erkennt.
Harry Fast, wissenschaftlicher Mitarbeiter am Fraunhofer IOSB-INA erläutert: „Durch unsere enge Zusammenarbeit mit Weier und seinen Kunden haben wir festgestellt, dass der Verschleißprozess bei verschiedenen Unternehmen unterschiedlich schnell verläuft. Das liegt unter anderem an den individuellen Produktionsbedingungen. Deshalb wollten wir ein System schaffen, das Unternehmen dabei unterstützt, die Lebensdauer ihrer Füllkammern zu maximieren.“ Denn neben unvorhergesehenen Ausfällen kosten auch zu früh ausgetauschte Kammern Zeit und Geld.
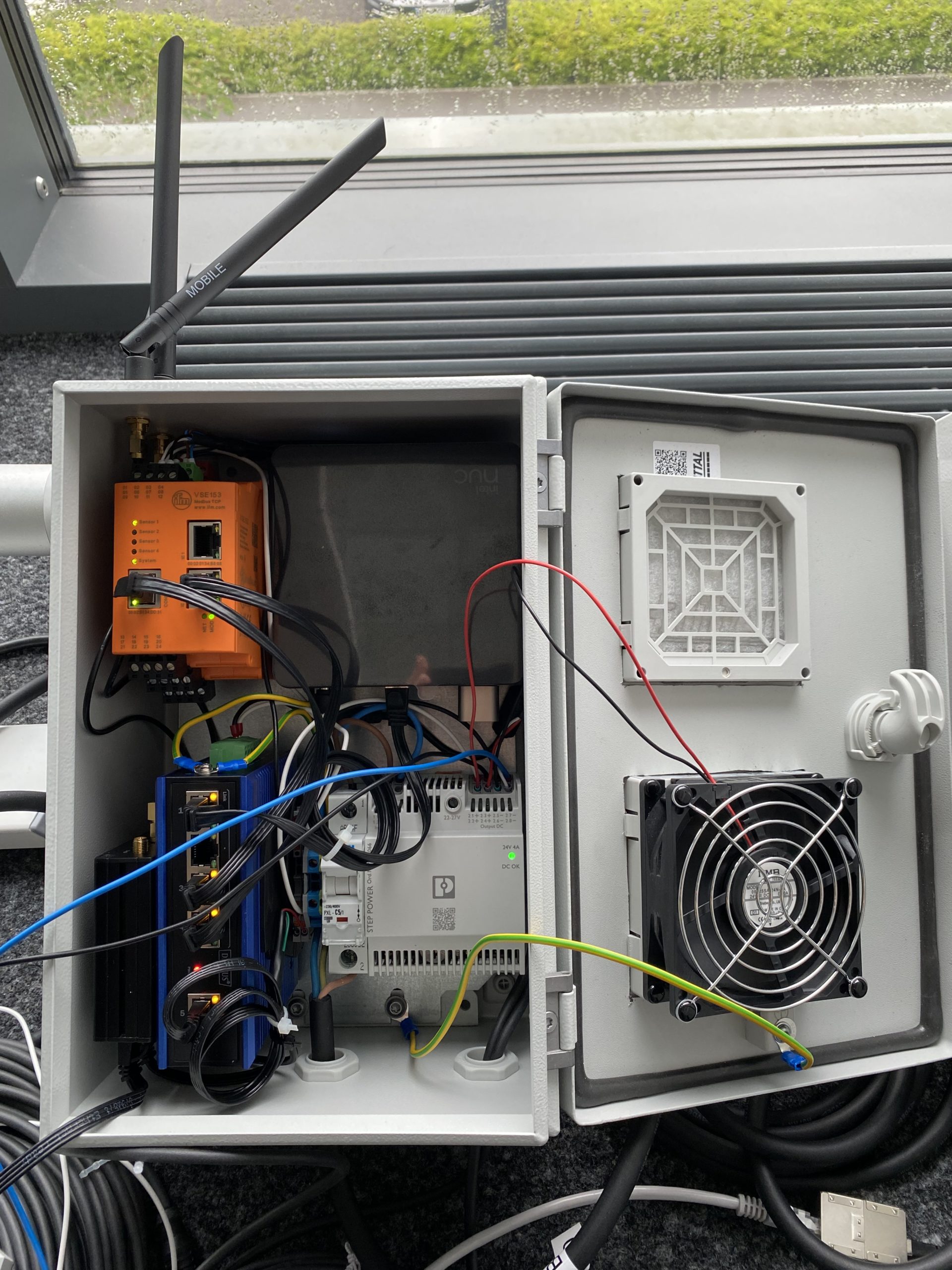
Mit Messboxen wie dieser werden die an den Maschinen gesammelten Daten aggregiert und kabellos an das Fraunhofer IOSB-INA in Lemgo übertragen. (Foto: Fraunhofer IOSB-INA)
Datensammlung
Messboxen liefern die Datengrundlage
Das Projektziel war klar definiert: Ein sensorgestütztes System sollte entwickelt werden, um den Verschleißprozess der Füllkammern auch aus der Ferne besser nachvollziehen und vorhersagen zu können. Dabei hat das Projektteam zunächst die Anforderungen festgelegt und ein Konzept entwickelt, wie ein solches System aussehen kann. Dazu gehörte die Auswahl der Sensoren, die Plattform zur Datenverarbeitung sowie die gesamte Architektur der Lösung.
Das Herzstück des Projekts war die Entwicklung sogenannter „Messboxen“, die bei drei Kunden von Weier installiert wurden. Diese Boxen sammelten über einen Zeitraum von fünf Monaten zuverlässig Schwingungsdaten, die durch die Bewegungen in den Füllkammern entstehen. Diese Daten wurden per LTE ins Lemgoer Fraunhofer Institut übertragen. Hier bildeten sie die Grundlage für ein KI-Modell, das den Verschleißprozess vorhersagen sollte – waren gleichzeitig aber auch eine der größten Herausforderungen des Projekts: „Wir wussten, dass viele Daten zusammenkommen würden. Die Verarbeitung erforderte eine sorgfältige Planung und war recht zeitaufwändig“, sagt Fast. „Trotzdem konnten wir hier dank der stabilen Übertragung zu einem guten Ergebnis kommen.“
Eine weitere Hürde stellte das sogenannte „Labeling“ dar – die Zuordnung der erfassten Daten zu bestimmten Zuständen der Füllkammer: Zum Zeitpunkt der Aufzeichnung wurde kein direkter Zusammenhang zu den Schwingungsdaten aufgestellt. Das Unternehmen musste den Kammerzustand selbst bewerten bzw. Events wie den Qualitätsabfall dokumentieren. Die Korrelation mit den Schwingungsdaten sollte dann über das KI-Modell gelernt werden.
Trotz dieser Herausforderungen konnte das Team beeindruckende Ergebnisse erzielen: „Rückblickend betrachtet haben wir eine Genauigkeit von 95 % erreicht, wenn es darum ging, den Verschleißprozess einer einzelnen Kammer vorherzusagen“, berichtet Fast. Die Übertragbarkeit der Modelle auf andere Füllkammern stellte sich jedoch als schwierig heraus. „Während wir für eine Kammer sehr präzise Vorhersagen treffen konnten, lag die Trefferquote bei der Vorhersage für andere Kammern nur noch bei 50 %. Das zeigt uns, dass wir noch mehr Daten benötigen, um das Modell weiter zu verbessern.“
Ausblick
Mehr Daten, bessere Ergebnisse
Die gewonnenen Erkenntnisse sind für Weier und die beteiligten Unternehmen eine wichtige Grundlage, um die Instandsetzung der Füllkammern weiter zu optimieren. So plant das Projektteam etwa, noch mehr Daten zu sammeln und das KI-Modell weiter zu trainieren. Auch könnten die Rohdaten noch feiner analysiert werden, um zusätzliche Informationen zu gewinnen.
Darüber hinaus könnte das entwickelte System auch in anderen Bereichen eingesetzt werden, erläutert Fast: „Die Messboxen sind so konzipiert, dass sie auch in anderen Verschleißprozessen genutzt werden können. Verschleißprozesse lassen sich oft durch Schwingungsanalysen erkennen, was uns viele weitere Anwendungsmöglichkeiten eröffnet.“
Die Kooperation zwischen der Weier GmbH und dem Mittelstand-Digital Zentrum Ruhr-OWL hat gezeigt, wie vielseitig und wertvoll die Digitalisierung für mittelständische Unternehmen ist. „Wir haben hier einen wichtigen Grundstein gelegt“, fasst Justin Wagner zusammen. „Auch wenn es noch Herausforderungen gibt, sind wir auf einem guten Weg. Die gewonnenen Daten und Erkenntnisse werden uns helfen, den Verschleiß von Füllkammern noch besser zu überwachen und so die Effizienz weiter zu steigern.“
Was hat´s gebracht?
Die Vorteile
- Proof of Concept für die KI-gestützte Ausfallvorhersage
- Grundstein für neuen Service
- Verstärkte Kundenbindung durch Erweiterung des Geschäftsmodells Instandsetzung
Sie wollen ebenfalls eine Erfolgsgeschichte schreiben?
Dann schreiben Sie doch zuerst einmal uns.