Erfolgsgeschichten
Digitale Transformation
Pressteile produzieren - mit (neuem) System
Bruse organisiert die Fertigung neu und digitalisiert die Prozesse
Ergonomische Montage-Arbeitsplätze und ein neues Transportbehälter-Konzept: Das sind zwei von mehreren Bausteinen der Fertigungsoptimierung, die der Pressteil-Hersteller Bruse in Attendorn verwirklicht und damit die Produktionprozesse deutlich effizienter gestaltet hat – mit Unterstützung des Fraunhofer IML.
Wenn ein vor mehr als 130 Jahren gegründeter mittelständischer Hersteller von Pressteilen aus Messing und Aluminium zu den Marktführern in seinem Geschäftsfeld gehört, 165 Mitarbeiter beschäftigt und wiederum marktführende Unternehmen beliefert – dann hat er in der Vergangenheit offenbar einiges richtig gemacht. Dazu gehört bei der Bruse GmbH & Co. KG in Attendorn die Fähigkeit, die Fertigungs- und Organisationsprozesse immer wieder an neue Anforderungen anzupassen und dabei auch Expertise von außen einzuholen – ganz aktuell in einem Projekt des Mittelstand-Zentrums Digital Ruhr-OWL.
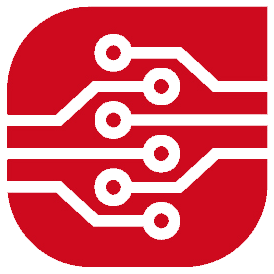
Digitalisierung als Herausforderung
Anknüpfung an Vorarbeit
Gute Basis für die weitere Optimierung des Materialflusses
In einem vorangegangenen Projekt hatten die beiden Beteiligten – Bruse und Fraunhofer IML – bereits eine umfassende Neustrukturierung der Produktionsprozesse geplant und systematisch umgesetzt. Nach dem Motto „Pull statt Push“ wurde der Materialfluss deutlich effizienter gestaltet und das Fertigungskonzept um die Produktion von Halbfertigwaren ergänzt, die bei Bedarf schnell kundenspezifisch konfiguriert werden können. Auf dieser guten Basis konnten die Akteure des „Transformation Coach“-Projektes jetzt aufbauen und sich dabei auf Workflow-Verbesserungen in der Endmontage und der Logistik konzentrieren.
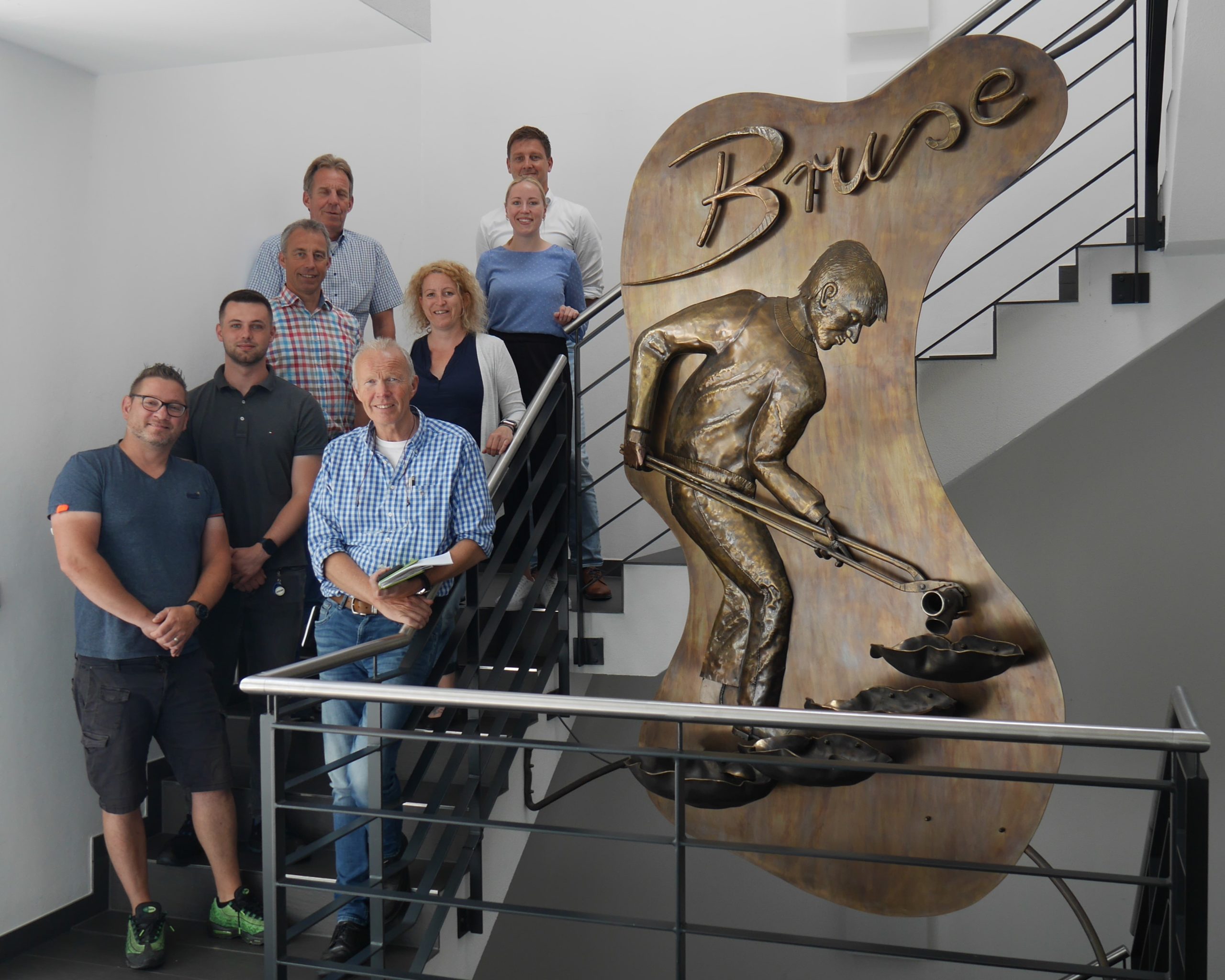
Umsetzung in die Praxis
Kleinere Behälter - verbesserte Handhabung
Nachdem die effiziente Belieferung der einzelnen Montage-Arbeitsplätze per Routenzug schon im ersten Projekt geplant wurde, erarbeitete das Projektteam ein neues Behälterkonzept. Der Materialtransport der Pressteile zu den Montage-Arbeitsplätzen erfolgt dann nicht mehr in großen und bis zu 70 kg schweren Gitterkörben, sondern in stapelbaren Kunststoffbehältern (KLT), von denen drei Größen im Umlauf sind.
Zugleich werden die Teile dann stückzahlgenau und, gemäß dem neuen Produktionskonzept, teilweise vormontiert an die Montage geliefert. Das vereinfacht aus Sicht des Personals die Handhabung. Nach erfolgreicher Erprobung an einem ersten Test-Arbeitsplatz wird dieses Prinzip in Kürze in der gesamten Montage umgesetzt.
Ergonomie im Fokus
Pilot-Arbeitsplatz in der Endmontage
Aus Sicht der Projektverantwortlichen von Bruse und auch des IML gehört es zu den Erfolgsfaktoren, die Mitarbeiter weitgehend einzubeziehen – auch (aber nicht nur), um deren Praxiswissen zu berücksichtigen.
Bei Bruse waren insgesamt zwölf Mitarbeitende in mehreren Teilprojekten beteiligt – und das Unternehmen zieht eine durchweg positive Bilanz. Geschäftsführer Christian Bruse: „Mit dem neuen Konzept für unseren Standort in Attendorn machen wir einen großen Innovationssprung. Unsere Produktion wird in Zukunft deutlich flexibler, effizienter und schneller sein.“
Das Projekt geht weiter
„Hilfe zur Selbsthilfe “
Auch wenn das „Transformation Coach“-Projekt nach insgesamt zwölf arbeitsintensiven Workshops abgeschlossen sein wird, geht die Transformation bei Bruse weiter. Denn diese Projekte sind von vorneherein so angelegt, dass das beteiligte Unternehmen sie in Eigenregie weiterführen kann. Das Know-how ist – dank des Projektes – jetzt vorhanden, die entsprechende Roadmap wurde gemeinsam erstellt.
Was hat´s gebracht?
Die Vorteile
- Prozessverbesserung
- mehr Innovation im Unternehmen
- zukunftsfähig
Sie wollen ebenfalls eine Erfolgsgeschichte schreiben?
Dann schreiben Sie doch zuerst einmal uns.